ICF Blocks with Recycled PVC Core
Revolutionary Building System which is faster, lightweight , stronger and less expensive than conventional build systems. System uses recycled PVC together with high density VSP foam panel which forms a hollow wall cavity, insulation and vapour barrier . Micro-rebar (Helix) is added to the concrete in the concrete truck for strength, resilience and avoids rebar tying.
Product Approach
/01
Tried
Insu-Built product was developed over 5 years and tested in the harshest environment with the most onerous conditions for seismic, wind,excessive rainfall ( NW coast of US and Canada )
/02
Tested & Approved
In fact the Insu-Built system is one of the few building systems that meets the new BC Building Code for sustainability, energy savings and environment friendly construction.
/03
True
It is designed to withstand 120 mph winds and heavy rains and is ideal in very hot, wet, and extreme cold conditions while maintaining a comfortable indoor living environment.
4 Plex Residential Multifamily Design Example
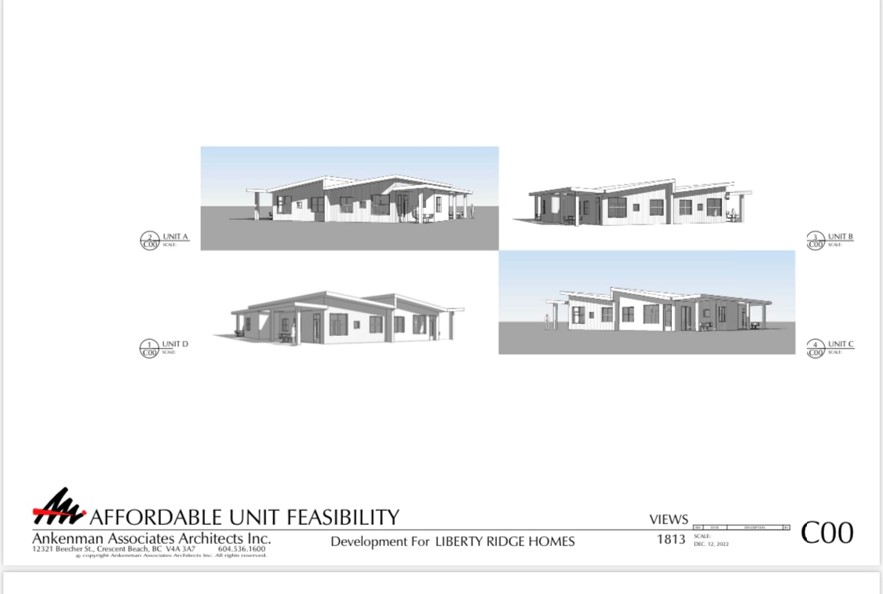
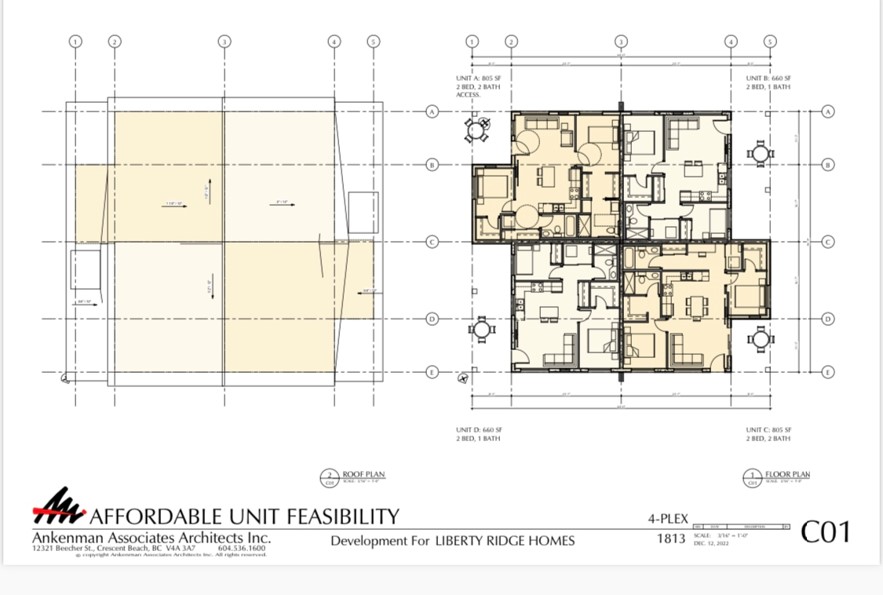
Insu-Built
Features and Benefits
Ease of assembly
The slide-and-clip methodology for the product allows for both build-in-place and prefabrication of wall assemblies, reducing overall construction time by more than 50%.
The same product and process are used both for below and above-grade applications, which means that only one crew needs to be deployed and coordinated throughout the construction of the structure.
The exterior VSP (Vertical Styrofoam Panel) has a permeable air barrier already affixed, as well as an integrated rain screen. This eliminates going around the structures additional times to install third-party exterior air barrier material and a 5/8” rain-screen. Once the wall is assembled, it is ready for concrete and finishing.
The interior VSP has a vapor barrier attached. This allows for the attaching of drywall directly to the I-Beam flanges without any further additional product and sealing being required.
Electrical is cut into the interior 3” thick VSP with a “hot knife”, eliminating drilling through multiple studs while maintaining an airtight seal with the remaining Styrofoam behind the etched VSP.
Plumbing is preinstalled in the wall cavity formed between the interior and exterior VSP assemblies, similar to a commercial construction. Again, much time is saved as there is little to no drilling required other than for stubbing out of the interior VSP for drains, venting, and waterlines.
Ventilation efficiency is greatly increased while operational costs to operate are reduced by upwards of 60%. This is achieved by the virtually airtight envelope that the VSP forms once the Helix-reinforced concrete is poured into the wall cavity. Heat, cooling, and humidity are all fully controllable from inside the constructed unit. Far smaller heating and cooling units are required, and their life cycle is greatly enhanced as there is far less cycling on and off for both the heating and cooling components.
Assembly timeframes for multi-story structures are greatly reduced as floor assemblies can be installed concurrently with the completion of one floor of the wall assembly and the commencement of the next floor’s wall assembly. Depending on the design, a 6plex of three-story townhouses can be at lockup in 8-10 days. This allows for trades to get onto the finishing stages weeks and months earlier than with conventional framing, getting the product to market months and in some instances, years earlier than previously possible.
(Vertical Styrofoam Panels)